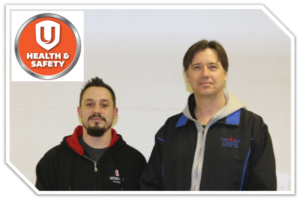
What’s that in the Washroom?
On January 16, 2020, we responded to a call from a worker in the Tool room on the 3rd floor who was concerned about the cleanliness of their washroom. We’ve received many similar calls recently and have responded to all accordingly. This call was a little different in that two co-workers working in the same area were both displaying similar symptoms typical of a common contagious fungal skin condition.
The concern was documented on their Level 5 Board, and they discussed their concern with their other co-workers at the next morning’s SOS meeting. After the meeting 2 additional workers came forward to announce they were also experiencing rash like symptoms. Although these four workers symptoms may be unrelated, facilities cleanliness has been an ongoing issue throughout the plant. So, they began putting 2 and 2 together and discovered they all shared the same facilities, notably the 4th floor team room for their SOS, the 3rd floor and 4th floor wash rooms, and the west shower room. Our investigation of these facilities revealed evidence that could be considered unsanitary.
The KFM issue has been discussed in the JHSC twice since 2006, and we wanted a quick resolve to reinforce countermeasures already promised. So, we chose to file a Health and Safety Complaint (grievance) to protest General Motors for failing to provide adequate resources, training and oversight to ensure that Knight Facilities Management follow and maintain the St. Catharines Restroom Cleaning and Locker room Cleaning Standards. A H&S Complaint goes directly to the third step of the Grievance procedure engaging our Plant Chairperson. This also engaged KFM’s Regional Manager, bringing him to our plant to investigate and help resolve.
Let us be perfectly clear. This is not a complaint against KFM workers, who we believe try and do their best while being told to do more with less, as are we all. Over the past 10 years KFM have reduced their number of janitorial employees, yet they are expected to maintain the same amount of work plus more. All we are asking is they be managed in a way that ensures they are following their standardized work, that they be given enough time to do this work completely while receiving adequate training to do this work safely, and if they are unable to complete their standardized work they be given a process to report and provide feedback to their managers, so adjustments can be made to maintain the standards.
During our discussions to resolve the grievance last week both companies admitted that standardized work was not being followed; that janitorial staff and G/Ls were not adequately trained; that site management was not holding hourly and salary employees accountable and that audit sheets are inadequate as they are product based, looking for soap and Pg.2 towels not performance based, focusing on cleanliness.
Corrective actions include: retraining all employees on job instructions; changing to use pre-approved chemicals for deeper cleaning and retraining employees for use; to purchase a disinfectant machine to spray restrooms monthly (this technique is used in NFL stadiums after home games); KFM site manager and Unifor H&S Rep to perform weekly quality audits, with audit sheet sign-off and feedback to KFM employee of findings; KFM G/L to review and retrain on acceptable and unacceptable conditions and audit the condition of assigned areas with employees on shift; KFM to develop a deep cleaning schedule for rest room and shower facilities throughout the plant; and to use scented urinal screens to improve restroom odour.
The weekly audit sheets will also be revised to clearly state time and date cleaned, state daily required tasks, and if workers are unable to complete task, to mark an X with a note on the back of the sheet explaining why. The back of the sheet is where KFM employees are trained to report conditions in the facility that require escalation, such as HELP desk calls to Building Maintenance etc. If a bag is over a toilet, the explanation why should be on the back of the audit sheet. We will also trial a user survey, where users can report conditions.
The GM Matrix that clearly shows KFM and BT responsibilities has been updated and will be posted in each team room. KFM responsibilities for team rooms is weekly, and while the BTs daily responsibilities are unchanged, it will be the BT G/Ls who ensure they are met.
To address the Tool room workers Safety Concern, the 3rd and 4th Floor washrooms and team room received a deep clean over 2 shifts last weekend. We were given an opportunity to observe their process and we believe these facilities to be sanitary. Now we must maintain.
Your Union is opposed to Behaviour Based Safety programs that focus blame on the worker’s behaviour rather than the root cause of a hazard. However, when it comes to the cleanliness of our facility, the behavior of all hourly, salary and contractor, directly impacts our shared conditions. Therefore, all of us share some responsibility for keeping it clean. Anyone who doesn’t respect themselves or their facilities by dropping trash, by deliberately clogging toilets, urinals etc. for whatever reason only harm their fellow workers, GM plumbers, and the good workers of KFM who are literally asked to polish a turd every day. If you think you’re harming the company or KFM, you are not. You are only making a bad situation worse for everyone. If you have an issue, whatever it is, that’s not being addressed please call us, so we can help.
Please respect yourself, your co-workers and your workplace.
Unifor Health and Safety Rep Edward Steers, 905 641 6420, Cell/Text 905 658 3271, ed.steers@gm.com
Alternate Unifor Health and Safety Rep Mike Pagano, 905 641 6505, PTT 7440029, mike.pagano@gm.com